Industrial Applications
Endlas Performance
Endlas Capabilities
Endlas Performance
Industrial Applications
Endlas Performance
Endlas Capabilities
Endlas Performance
Endlas Performance
Endlas Capabilities
Endlas Performance
Endlas Performance
Endlas Capabilities
Endlas Performance
Endlas Performance
Endlas Capabilities
Endlas Capabilities
Endlas Capabilities
Endlas Capabilities
Redefining Material Possibilities

Laser Processing
Lasers offer significant benefits for a variety of material
thermal processing applications. Using laser energy for
processing materials is highly preferred for
many situations because it is rapid, non-contact, and a
highly controllable radiant heating method as compared
to traditional heating methods. Some of the most common
applications for lasers in material processing include: heat
treatment, and surface glazing.
Laser Heat Treatment
Laser heat treating uses highly controlled laser energy to direct precise heat output to a selected area of a metal component’s surface to achieve transformation temperatures, which quickly cools to the desired microsturcture. The product of rapid heat removal results in a phenomena called self-quenching.
Self-quenching removes the need for oils and other quenching media, reducing the environmental burden of traditional heat treatment processes. Controlling the speed of the beam can produce a case hardening on the surface tailored to the application needs. All stages of heat treatment (hardening, case hardening, annealing, normalizing, and tempering) can be replicated using our laser heat treatment process.
Laser Glazing
Laser glazing is a surface-melting technique in which a continuous, high-energy, laser beam traverses the surface of a metal part, creating a thin layer of melted material. After the laser-glazing process, the material's surface appears glassy.
Laser glazing can produce surfaces which are amorphous, glassy, or non-crystalline in structure. Laser glazing provides excellent wear resistance, and an enhanced corrosion resistance, through the formation of phases typically not achieved through traditional forging and heat treatment methods. No post processing is required as the highly controllable laser beam provides selective melting at the precise depth and location needed.
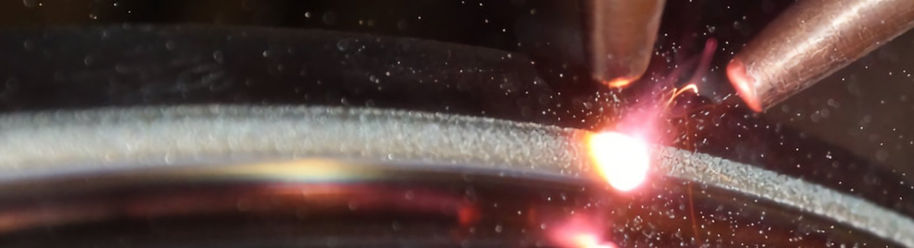

